NEWS
Heat Shrink Tubing: Extreme Environment Use
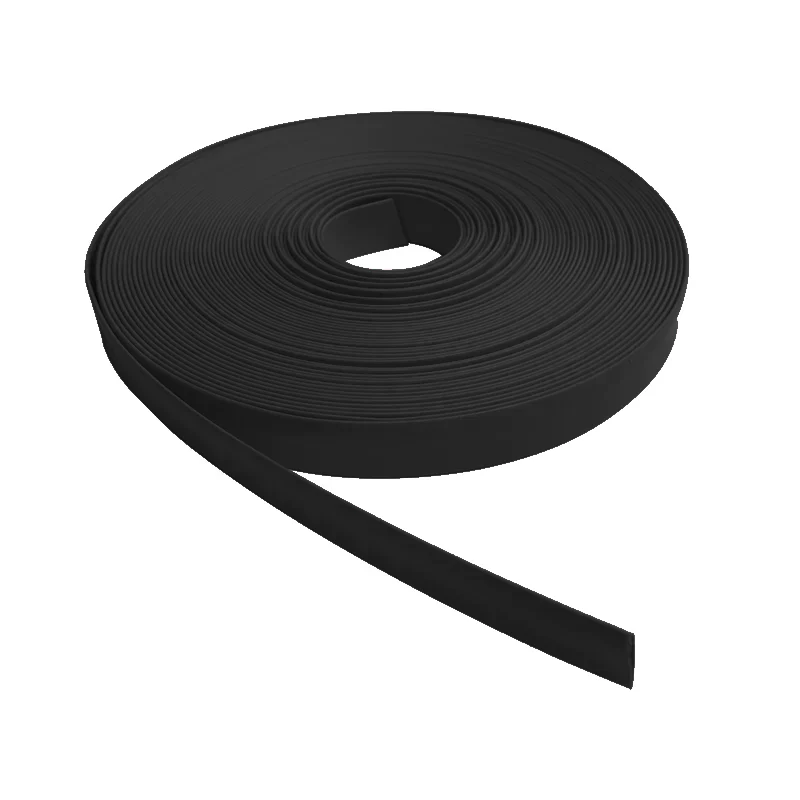
In industries where environmental resistance, durability, and insulation are critical, heat shrink tubing is an indispensable component. Designed to provide superior protection against harsh conditions, heat shrink tubing is widely used in aerospace, automotive, marine, and industrial applications. In extreme environments, where exposure to high temperatures, chemicals, moisture, and mechanical stress is common, selecting the right heat shrink tubing is vital to ensuring long-term reliability and performance.
Why Use Heat-Shrink Tubing in Severe Conditions?
Heat shrink tubing is an essential protective layer for wires, cables, and other components in harsh environments. The primary benefits include:
1. Protection Against High Temperatures
Electrical components are frequently exposed to high temperatures in sectors like energy production, automotive, and aerospace. High temperature heat shrink tubing, made from materials like polyolefin, PTFE, or fluoropolymer, can withstand temperatures exceeding 250°C, ensuring insulation and preventing wire degradation.
2. Chemical and Corrosion Resistance
Exposure to corrosive substances is unavoidable in oil refineries, chemical plants, and maritime environments. Heat shrink tubing with chemical-resistant properties shields electrical components from solvents, acids, oils, and other hazardous materials, prolonging their lifespan and functionality.
3. Moisture and Waterproofing Capabilities
Heat shrink tubing with an adhesive-lined interior offers a waterproof seal in applications subjected to moisture, humidity, or submersion, such as underwater cable installations and marine environments. This prevents moisture ingress, which can lead to electrical failures or corrosion over time.
4. Mechanical Strength and Abrasion Resistance
Heavy machinery, industrial automation, and aerospace applications require insulation that can endure mechanical stress, vibration, and physical wear. Heat shrink tubing made from durable materials like elastomeric or dual wall constructions offers superior abrasion resistance, preventing damage to wires and connectors.
5. Electrical Insulation and Safety
Proper insulation is essential to prevent short circuits, electrical arcing, and safety hazards in high-voltage environments. Heat shrink tubing with high dielectric strength enhances insulation and safeguards against electrical failures, ensuring operational safety in mission-critical applications.
Key Industries Utilizing Extreme Environment Heat Shrink Tubing
Aerospace and Defense
Aircraft wiring and military-grade electronics require heat shrink tubing that withstands high altitudes, temperature fluctuations, and mechanical vibrations. Specialized heat shrink tubing meets MIL-SPEC (Military Specifications) standards, ensuring reliability in defense applications.
Automotive and Motorsport
Heat shrink tubing that can withstand high temperatures, oils, and vibrations is required for automotive applications ranging from sensor wiring to engine compartments. Electrical connections and wiring harnesses in performance cars and heavy-duty trucks are shielded by flame-retardant and fuel-resistant tubing.
Marine and Offshore
Saltwater exposure, humidity, and harsh weather conditions necessitate the use of heat shrink tubing with waterproof and UV-resistant properties. This ensures durability in offshore drilling, shipbuilding, and underwater cable applications.
Energy and Power Distribution
Renewable energy installations, power grids, and electrical substations require insulation that withstands extreme weather conditions, UV radiation, and electrical stress. Heat shrink tubing designed for high-voltage applications enhances safety and longevity in these environments.
Choosing the Right Heat Shrink Tubing for Extreme Conditions
When selecting heat shrink tubing for demanding environments, consider the following factors:
- Material Composition: Polyolefin, fluoropolymers (PTFE, FEP), elastomers, and dual-wall tubing provide varying levels of heat, chemical, and mechanical resistance.
- Shrink Ratio: A higher shrink ratio (e.g., 3:1 or 4:1) allows for a snug fit around irregularly shaped components.
- Operating Temperature Range: Ensure the tubing can withstand the lowest and highest temperature extremes of the application.
- Adhesive-Lined vs. Standard Tubing: Adhesive-lined (dual-wall) tubing provides an additional waterproof seal, ideal for marine and outdoor applications.
- Compliance and Standards: Look for tubing that meets relevant safety and industry standards, such as MIL-SPEC, UL (Underwriters Laboratories), and ASTM (American Society for Testing and Materials) certifications.
Heat shrink tubing is a crucial solution for protecting electrical components in extreme environments. Whether dealing with high temperatures, harsh chemicals, moisture, or mechanical stress, selecting the appropriate heat shrink tubing ensures safety, reliability, and longevity. Industries such as aerospace, automotive, marine, and energy depend on advanced tubing solutions to maintain operational efficiency. By choosing heat shrink tubing that meets industry standards and application requirements, businesses can enhance the durability and performance of their electrical systems in even the most challenging conditions.
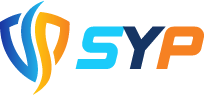